Alternative Materials to Portland cement: geopolymers
The study and development of new cementitious materials alternative to Portland cement is a line of priority research and of great interest worldwide, where, with the development of these new materials is intended to minimize as much as possible the emissions of polluting gases to the atmosphere as well as appreciable energy savings.
Within these alternative materials are those that come from the alkaline activation of natural products or industrial by-products, such as blast furnace slag and / or the fly ash, where after the activation of these materials with alkaline solutions these materials are obtained . These alkaline cements and concretes are characterized by low levels of hydration, high mechanical performance, and good durability against different aggressive chemicals (acid, sulfuric media, etc.), and do not require high energy consumption in their processing, as is the case with the process Portland cement manufacturing. The alkaline activators used are strongly alkaline solutions (NaOH, Na2CO3 or hydrated alkaline silicates).
In our research group we work on establishing the scientific basis for a better understanding of each and every one of the mechanisms involved in the activation of different materials, as well as in the physical, chemical, mechanical and mineralogical characterization of the main products of formed reactions, through the use of different characterization techniques, highlighting Confocal Raman Microscopy.
- Development of pastes, mortars and concretes activated alkaline and / or geopolymer of fly ash and blast furnace slag.
- Development of new cementitious materials and alternative activators from industrial waste or byproducts, student the feasibility of these residues as possible precursors.
- Study and development of hybrid cements (OPC + slag + ash)
- Study of the durability of these materials against different aggressive agents (sulfates, chlorides, carbonation, etc.) as well as the corrosion phenomena in the reinforcements (different types of steel).
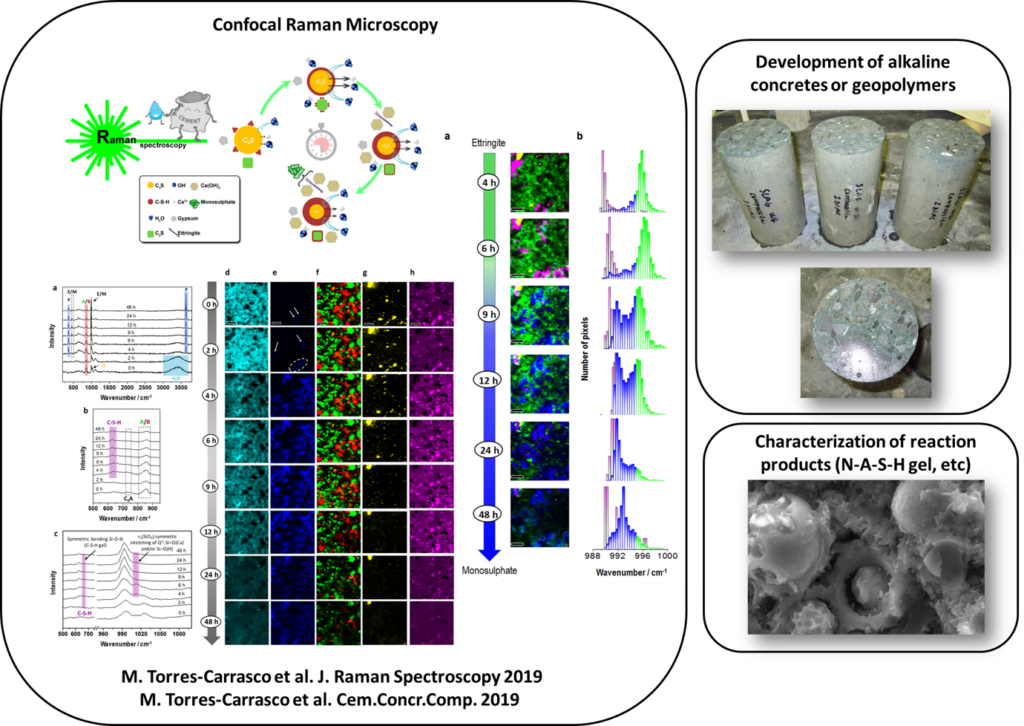
This research line is developed in following areas:
Surface treatments and adhesion: adhesives, paints and coatings
This research line has been developed to solve adhesion problems usually taking place in industrial applications, when components have to be bonded and/or painted. Environmentally friendly surface treatments are adapted to different surface, taking into account the curing process of the adhesive, Paint or coating. Moreover, simulations of adhesive bonds and durability tests under aggressive environments are carried out. This way, new applications for materials can be found on different substrates.
- Improvement of the adhesion of paints and adhesives to substrates modified with plasma.
- Reduction of adhesion ability of surfaces: antigrafitti treatments, demoulding agents, superhydrophobic surfaces.
- Mechanical performance and reliability of tough flexible adhesives in aggressive environments, and their use in structures standing vibrations and impacts.
- Development of adhesive bonds between dissimilar materials with structural applications.
- Thermal behaviour and curing kinetics of functionalized (modified) resins.
- Simulating and optimizing graded adhesive bonds.
- Bone cements (methacrylate based adhesives) with different loads.
This research line is strongly bonded to composite materials, as many adhesives are used as matrixes, and bonding to reinforcements is an adhesion issue.
Corrosion
In-service materials performance research group has huge experience regarding durability studies on metallic materials, quantifying corrosion rate using electrochemical techniques. Moreover, the group uses adequate techniques to evaluate (with accuracy and reliability) critical aspects for in-service performance as the exact morphology of the attack. We have resources and knowledge adequate to design and evaluate protection alternatives for metals in chemically aggressive environments.
Our experience in corrosion studies allow us the collaboration with companies to analyse service failures related to corrosion, and characterize the durability of new materials, coatings, designs, trade strategies as well. The use of both electrochemical techniques and accelerated tests is required for it.
On the other hand, researchers in the group has carried out innovative scientific studies. Focusing on last years, following areas can be pointed out:
- Design of corrosion cells with gel electrolytes adequate for in-situ monitoring and/or studies on surfaces with complex morphologies.
- Influence of the alkaline reserve of cements and the microstructure of carbon steel corrugated bar son the development of corrosion processes of reinforcements embedded in concrete.
- Durability of corrugated stainless steel reinforcements: influence of the chemical composition, processing and microstructure of the bars on the start and development of corrosion processes in mortars exposed to chloride containing environments.
- Influence of strain and stresses on the corrosion performance of austenitic and duplex stainless steels.
- Design of organic and inorganic coatings to assure the durability of components under aggressive environments.

Organic coatings
The degradation of metals due to corrosion is a problem implying economic and practical losses. Organic coatings are one of the most used methods to fight against corrosion. Wear resistance of those organic coatings is very important to avoid defects that can destroy the barrier effect and allow the development of the corrosion process in the base metal.
Nowadays, powder organic coatings are an alternative to conventional liquid paints. As main advantage, powder organic coatings do not present solvents in their composition, presenting environmental advantages. Another advantage is economic, as the material not bonded to substrate during coating process can be recovered up to 98%.
Another tendency is functionalizing coatings with nanoparticles to improve wear performance and hence corrosion protection. In-service materials performance research group is carrying out scientific studies with different coatings (epoxy and polyester based), SiO2 nanoparticles of different nature (hydrophilic and hydrophobic) and different mixing methods (mechanical milling and hot mixer). Studies developed to characterize and check the performance of powder organic coatings functionalized with nanoparticles are as follows:
- Morphological and homogeneity studies of nanoparticles in the matrix.
- Abrasive and erosive wear studies of organic coatings, together with their hardness and stiffness.
- Adhesion and roughness.
- Curing kinetics of powder coatings with nanoparticles.
- Aesthetical properties (colour and gloss).
- Corrosion studies.
Composite Materials
Nowadays, the use of composite materials as an alternative is expanding in different industries, from transport to sport material. Those materials offer good mechanical properties reducing weight meaningfully.
Hence, In-service materials performance group has developed this research line, working on polymer matrix composites. Studies on synthetic (glass, carbon…) and natural fibres (flax, coconut…), and hard particles as well (SiC, BN, marble …) have been carried out.
Moreover, studies on the recycling of composite materials are also being carried out, an area with a strong development in the scientific community.
With the knowledge of adhesion problems, exhaustive studies on matrix-reinforcement interface and adhesion are done. Several tests can be drawn:
- Mechanical properties of composites: tensile, bending, impact …
- Surface treatment of fibres: APPT, LPP, silanizing…
- Characterization of interfaces, with adhesion and wettability studied: peeling, pull-off, pull-out, contact angle …
- Chemical characterization: DSC, FTIR, TGA…
- Topographic characterization: SEM, optic profilometer …
Other aspects in-service materials performance
The research group has collaborated in theoretical Works related to other areas of materials performance. Using finite element modelling, fracture mechanics of polymer composite materials has been analysed under impact loads, or the use of intensity of singular stress field (ISSF) has been employed to calculate stress concentration points in metal-polymer interactions.